Background
When handling cultural materials, professionals often wear gloves to protect their hands or the objects from deleterious effects of handling. Gloves prevent the transfer of oils and other metabolic products (including various salts) to the object. Conversely, cultural objects can contain toxins, and so gloves are a vital element of personal protective equipment for cultural heritage professionals (Neilson 2020).
Gloves can be made from synthetic materials like nitrile, neoprene, and butyl rubber, or natural materials like cotton or latex (which can also be made synthetically). Which gloves are appropriate to use depends on the setting and the objects being handled. Considerations include chemical resistance, durability, bulkiness, and skin health (OSHA 2004). This Case Study allows cultural heritage professionals to also consider the environmental impacts of glove manufacture, use, and disposal.
There are also variations within material categories. For example, Stephens et al (2022) studied nineteen brands of latex-free, powder-free, and disposable nitrile gloves to identify the brands with least corrosion potential for art objects (Stephens et al 2022). The rub tests showed more pitting and corrosion on metal tabs resulting from contact with some of the glove brands more than others. Although different glove brands showed varied test results on the metal tabs, in material terms they are quite similar and small differences between glove brands will likely not lead to significantly different environmental impacts from production and disposal.
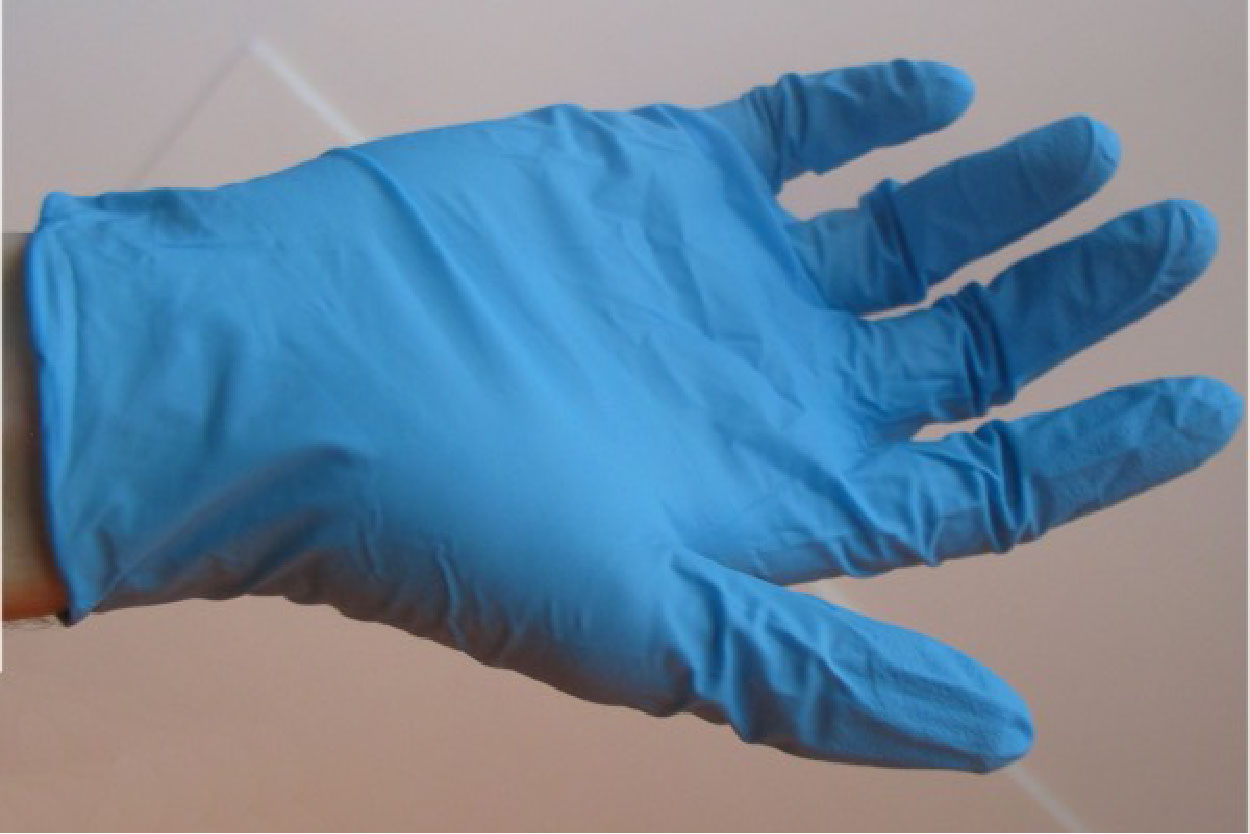
Nitrile gloves are thin and lightweight, allowing users to maintain dexterity for sensitive manual tasks. They are made of a polymeric synthetic material and are resistant to chlorinated solvents, but are not recommended for use with strong oxidizing agents, aromatic solvents, or ketones. They are available as powdered or not powdered, and sterile (individually wrapped and each glove checked for leakage) or non-sterile (100 to a box and only one glove per batch checked for leakage). Because of their versatility and low cost, nitrile gloves are popular across a wide range of cultural heritage settings. They are designed to be single-use.
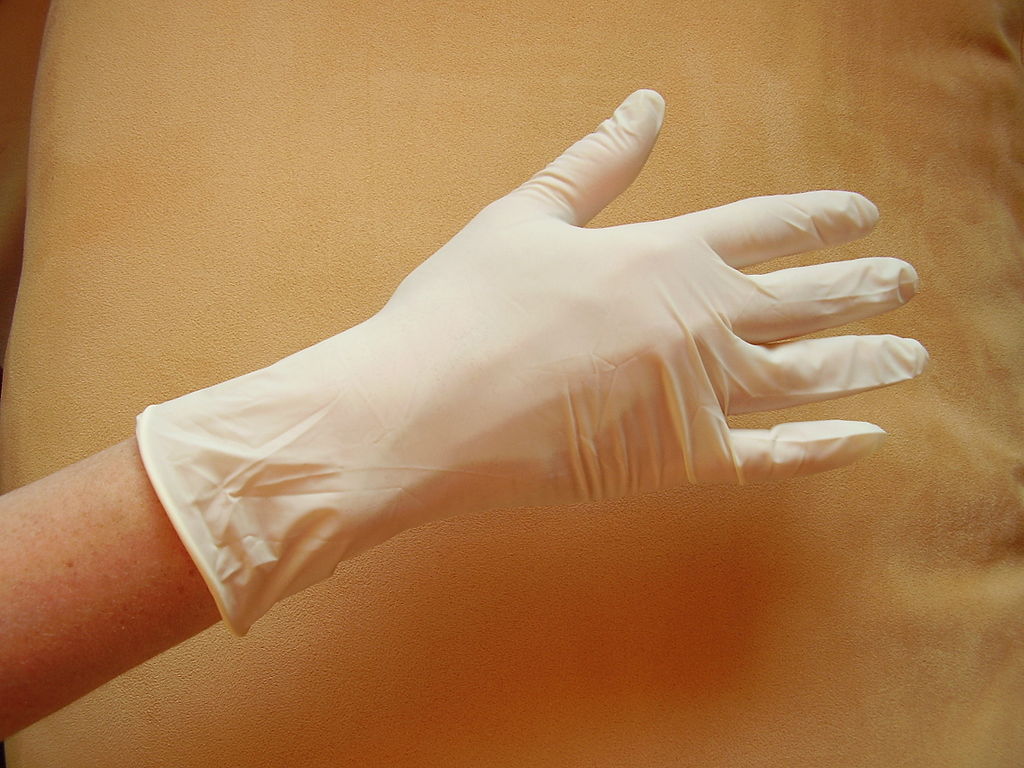
Latex glove. Werneuchen
Latex gloves are made of a natural or synthetic latex rubber, are thin and lightweight, and offer high tensile strength and elasticity. They are abrasion resistant and comfortable to wear. Latex offers different chemical resistance to nitrile: latex provides good protection against ketones such as acetone, but generally poor resistance to oils and chlorinated solvents. Some people have allergic reactions to latex, and so these gloves are not appropriate for all users. They are designed to be single-use. Natural latex is biodegradable.
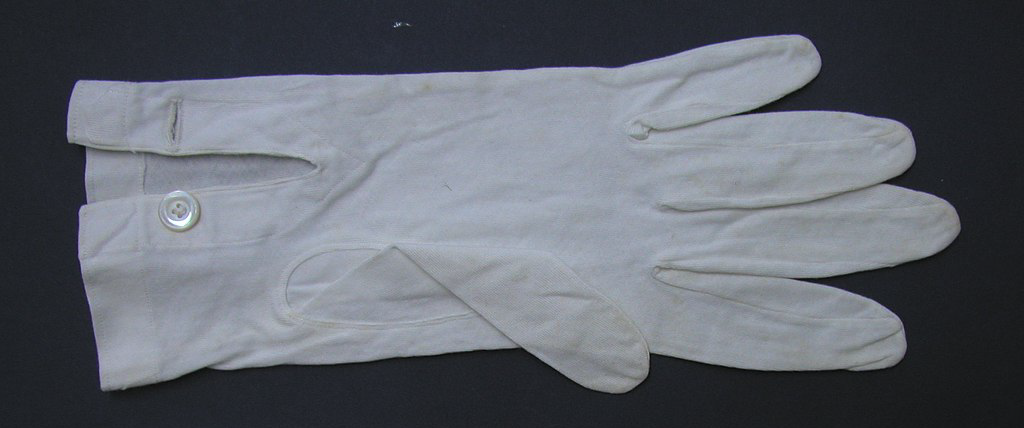
Cotton Gloves. Auckland Museum, CC BY 4.0
Cotton gloves are made of natural cotton fibers. Once used widely throughout the cultural heritage profession, we now understand that they carry a number of disadvantages. Cotton gloves are relatively bulky and can reduce dexterity. The cloth can snag on rough objects, or can not provide the necessary grip for handling smooth objects. As a natural fiber, cotton readily absorbs chemicals that it comes into contact with, which can then be transferred to objects. Cotton also offers little protection against many types of treatment chemicals or hazardous materials. Cotton gloves can be washed and reused. Washing should be done under mild conditions using soaps or detergents with minimal additives (Neilson 2020).
GENERAL SUSTAINABILITY CONCERNS
Because of their ubiquity in the cultural heritage profession and the need for frequent changes due to contamination, sweat, or task transitions, the use and disposal of gloves is highly noticeable (de Silva and Henderson 2011). Sustainability-minded practitioners have been publicly pushing for more information on the environmental impacts of gloves (Southwick 2019), particularly at museums with a science or environmental mission. As noted by Warden and Franz (2020): “Museums recognize their responsibility to educate and promote sustainability in the public sphere, so alternative products should be tested and everyday practices should be reviewed to determine their environmental impact.” In response, many institutions have instituted glove reuse and recycling schemes that accompany educational campaigns (Sutton and Wylie 2013). Manufacturers have also responded by instituting take-back programs so that glove materials can be incorporated into new products, promoting a “circular economy” (Kimberly-Clark 2022; TerraCycle 2022).
The cultural heritage sector is far from alone in its reliance on protective gloves, and its use is small compared to other sectors such as laboratories, food service or, especially, health care. The COVID-19 pandemic saw an explosion in the use of PPE in health care, raising questions about the sustainability of various options. Gloves differ in terms of their raw materials, production, use, and environmental consequences of different disposal options. Researchers have examined various types of gloves used in health care, often in the context of a particular care setting or procedure (Jamal et al. 2021; Rizan et al. 2021), typically finding that manufacturing is the largest contributor to environmental impacts of the life cycle of each glove option. Health care settings rely almost exclusively on nitrile or latex gloves, whereas cotton gloves are no longer used and so have not been studied as a comparative option. Cotton gloves can be washed and reused, and it is not immediately obvious which type of glove is environmentally preferable or how reuse changes the order of preference.
In this Case Study, we present a novel comparative environmental assessment for nitrile, latex, and cotton gloves used by cultural heritage professionals, supported by data gathered from a December 2020 AIC survey concerning glove use. The assessment explores end-of-life scenarios for each glove option, notably washing and reuse for cotton gloves and recycling or disposal for nitrile and latex gloves. The case study aims to provide information on the relative environmental performance of glove types and to support green procurement and waste management practices.
LCA Modeling
Life cycle assessment (LCA) is an internationally standardized (ISO 14040) modeling tool commonly used to quantify environmental and health impacts of a product or process (ISO 14040: 2006). LCA takes a holistic, systems approach by considering sustainability over the entire product life cycle, including raw materials extraction, manufacturing, transport, use, and end-of-life (Vigon et al. 2020; Fava and Society of Environmental Toxicology 1991; United Nations Environment Programme 2005). LCA has been implemented across all types of sectors to inform design and procurement decisions, and provides the scientific basis for all carbon, water, and environmental footprinting. For example, popular online calculators use LCA to compare different grades of paper or packaging materials (Environmental Paper Network 2021; sphera 2020).
For this case study, LCA modeling was completed using the free, open-source software OpenLCA (v1.10.3) with material-specific data from the ecoinvent database (v3.7, APOS) (Ecoinvent 2020; GreenDelta 2020). Global warming potential (or carbon footprint, measured in carbon dioxide equivalents, kg CO2 eq) and nine other categories of environmental and human health impacts for each scenario were calculated using the Tool for the Reduction and Assessment of Chemical and other environmental Impacts (TRACI v2.1) impact assessment method developed by the U.S. Environmental Protection Agency (EPA 2012). Further information concerning tools and methods can be found in the STiCH Introduction to LCA Information Sheet.
This case study covered a ‘cradle-to-grave’ scope (Figure 4), examining all life cycle stages of the products used to fulfill each scenario. LCA compares options based on the function that they provide – called a ‘functional unit’- ensuring fair comparisons. The functional unit for this case study was a single use of one medium-sized glove, in a generic situation where all three glove options are plausible choices in terms of performance.
Methods
In order to model the extent and patterns of glove use and management, the STiCH project in partnership with AIC conducted a member survey in December 2020, which garnered 135 responses. Table 1 summarizes the results of the survey for all three glove types. Nitrile was by far the most common glove type used by survey respondents, and all three types of gloves had some level of reported reuse. Cotton gloves could be reused several times, washed, and then reused again. In total, among respondents that reported reuse, cotton gloves were reused an average of 3.8 x 9.8 37 times. For modeling purposes, we round this number to 4 uses per wash and 10 lifetime washes, for a total or 40 uses per cotton glove.
This case study covered a ‘cradle-to-grave’ scope, examining all life cycle stages of the products used to fulfill each scenario (Figure 1). LCA compares options based on the function that they provide – called a ‘functional unit’- ensuring fair comparisons. The functional unit for this case study was a single use of one medium-sized glove, in a generic situation where all three glove options are plausible choices in terms of performance.
MODELING PROCESS
In order to model the extent and patterns of glove use and management, the STiCH project in partnership with AIC conducted a member survey in December 2020, which garnered 135 responses. Table 1 summarizes the results of the survey for all three glove types. Nitrile was by far the most common glove type used by survey respondents, and all three types of gloves had some level of reported reuse. Cotton gloves could be reused several times, washed, and then reused again. In total, among respondents that reported reuse, cotton gloves were reused an average of 3.8 x 9.8 about 37 times. For modeling purposes, we round this number to 4 uses per wash and 10 lifetime washes, for a total or 40 uses per cotton glove.
The LCA Modeling sub-sections describe the materials modeled for each category and their respective lifetimes; Table 1 summarizes this information.

Each glove type requires different materials and processes for manufacturing. LCA modeling requires information on the quantities and locations of each input and process step over the life cycle of a glove.
GLOVE MATERIALS AND MANUFACTURING
Nitrile gloves are produced from acrylonitrile butadiene rubber, an important synthetic rubber invented by the German chemical giant BASF in the 1930s as a replacement for expensive, far-away natural rubbers. Nitrile production is now concentrated in Korea and Japan. Raw nitrile rubber then makes its way to Malaysia, where most of the world’s nitrile gloves are made. Following Jamal et al. (2021), each glove requires 3.5 g of nitrile feedstock and 0.01 kWh of electricity for manufacturing and air-leak testing. Gloves are then packaged in containerboard boxes and then bulk packaged in cardboard (0.5 g per glove).
Latex gloves are derived from natural rubber, which is collected from rubber plantations largely located in Southeast Asia, or from synthetic latex. Natural rubber plantations are much less carbon-intensive than synthetic routes; here we assume that the plantation is long-running and thus exclude emissions associated with land use change. Latex is similarly transported to Malaysia for manufacturing. Latex gloves are slightly heavier than nitrile gloves; each glove requires 5 g of latex feedstock but undergoes essentially the same manufacturing and testing processes requiring 0.01 kWh (assuming non-sterile gloves; testing requirements for sterile latex gloves would increase energy requirements by a factor of 40). Latex gloves are packaged identically to nitrile gloves.
Cotton production is currently dominated by India and China, who produce approximately half of global supply. Cotton is the most water-intensive major crop, requiring more than 20,000 liters of water to grow one kg of fiber. In the mid-20th century, intensive cultivation of cotton in Central Asia led to the near disappearance of the Aral Sea, once the fourth largest body of freshwater on the planet and now approximately 10% of its original size. Cotton is picked, ginned, spun into thread, woven into fabric, treated (including bleaching), and finally cut and sewn into gloves. China is the largest producer of textiles and this study assumes that cotton glove manufacturing occurs there. Each glove requires 75 g of cotton fabric. Because cotton gloves are much bulkier than nitrile or latex gloves, they require approximately 5 times as much packaging material (2.5 g) per glove.
TRANSPORT
Since this case study is assessing representative supply chains and not specific brands or manufacturing locations, all gloves are assumed to undergo similar transportation steps with average distances commonly applied in LCA modeling. The final location where the gloves are used is also not specific. Gloves are assumed to be transported from their point of manufacturing 200 km to a coastal port, and then by oceanic freight to the West Coast of the USA from ports in Malaysia (14,000 km) and China (10,000 km). Gloves are transferred to trucks and transported an additional 500 km to a generic location.
USE AND DISPOSAL
Nitrile and latex gloves are assumed to be used once and then disposed of to landfill, which is the dominant waste management option in the USA. Alternate modeling scenarios of limited reuse, recycling, or incineration are also considered. Cotton gloves are assumed to be used multiple times and then washed on-site in warm water in a washing machine and dried in a dryer, which was the most common practice as determined by the 2020 AIC member survey. After final use, cotton gloves are also sent to landfill.
STUDY SCOPE
Figure 4 shows the overall system diagram of the study, including the various inputs, processes, and scenarios.
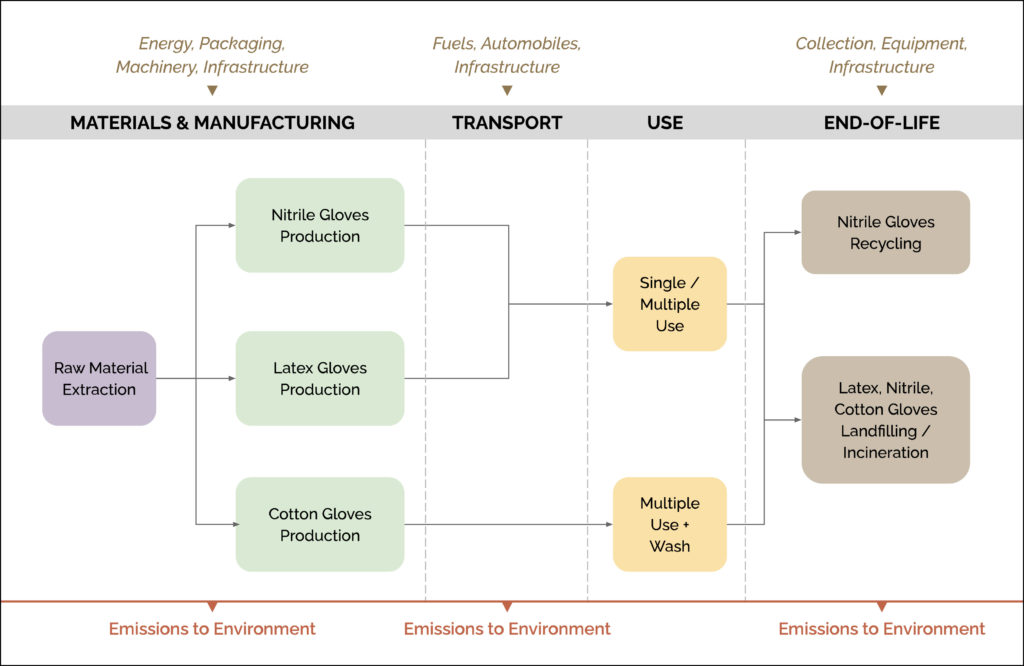
Results
Multiple sets of results are presented, corresponding to different patterns of glove use. First, Figure 5 shows the carbon footprint per glove of each material. This scenario represents the case where each glove is produced, used once and then discarded. Because of its much larger mass and the carbon intensity of cotton, the cotton glove has by far the largest footprint, more than 40 times that of nitrile. The natural latex glove has the smallest footprint due to the low carbon intensity of natural rubber (0.2 kg CO2 eq per kg of concentrated latex), despite the slightly higher mass compared to nitrile. Despite the fact that all gloves are manufactured in Asia and shipped more than 10,000 km to the USA, transportation accounts for a small share (10% or less) of overall carbon emissions, with the exception of natural latex gloves, which have low production emissions, thus raising transportation’s share of emissions to 20%. Emissions from waste management and disposal are even lower (3% or less in all cases).
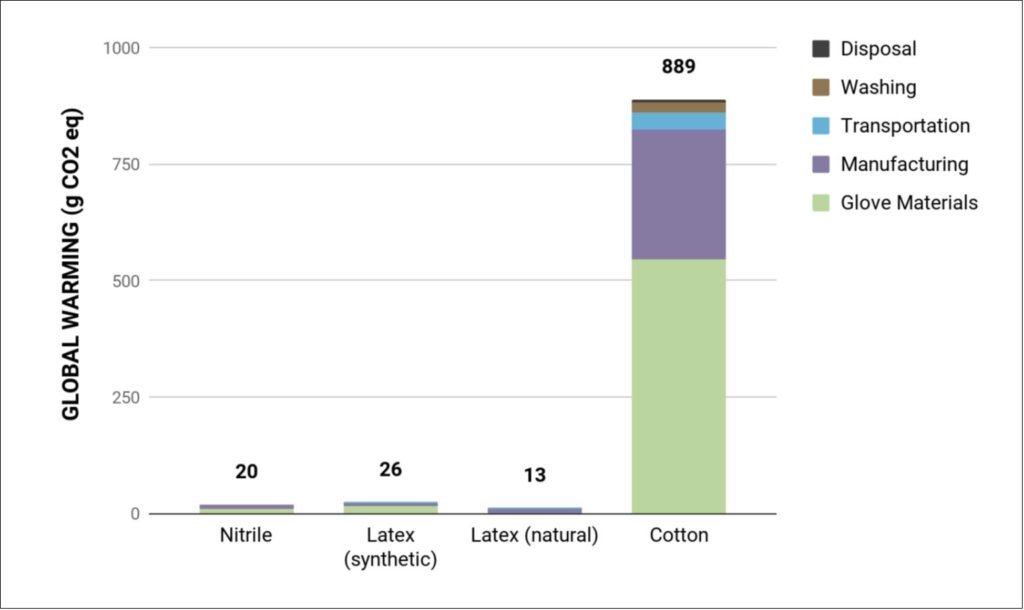
Next, Figure 6 presents results comparing each glove per use, assuming that the nitrile and latex gloves are used once and discarded, whereas the cotton glove is used 40 times, with a wash after every 4th use, as indicated by the 2020 AIC member survey. In this figure, there is an additional process of washing for the cotton glove, corresponding to emissions from pumping and heating water, manufacturing the detergent, and running the dryer. Repeatedly reusing and washing the cotton gloves dramatically lowers their carbon footprint, to the point where they are comparable to synthetic latex gloves. Natural latex gloves are still the preferred choice in this scenario, however.
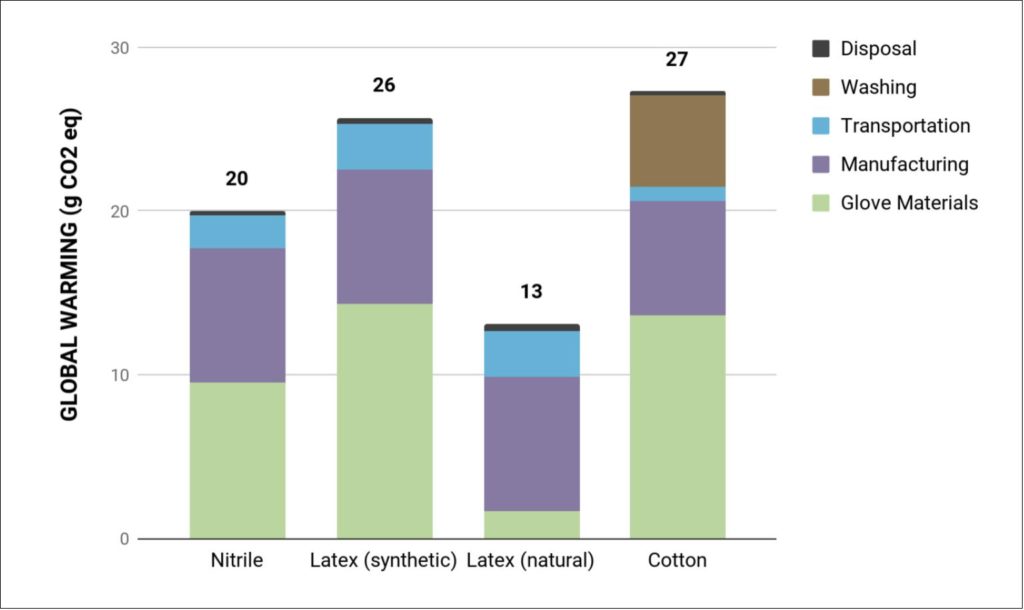
Changing how gloves are managed after use makes an important difference in their carbon footprints. If nitrile gloves are sent to incineration rather than landfill, this would increase their carbon emissions by more than 40%, to 28 g CO2 eq per use. This is because the carbon present in the synthetic materials does not appreciably degrade in a landfill, but when incinerated it is converted to CO2.
For cotton gloves, on the other hand, the carbon that is liberated from gloves during incineration is biogenic, meaning that it was originally sequestered from the atmosphere by the cotton plants during cultivation. These biogenic emissions from incineration do not count toward the carbon footprint because they are simply balancing the “negative emissions” from growing the cotton, resulting in net zero emissions. There are other emissions associated with collecting and transporting waste to the incinerator, as well as from natural gas that is used as a supplemental fuel in the incinerator, which count instead as fossil emissions from waste management. For typical municipal solid waste incineration, biogenic carbon emissions account for about 60% of the total. So, sending cotton gloves for incineration does lead to as significant an increase in carbon emissions as for the nitrile or synthetic latex gloves.
Many AIC members reported reusing nitrile and latex gloves, approximately twice for each before eventually discarding them to landfill. Doing so would reduce the carbon footprint of these options by approximately half, making them even more environmentally preferable compared to the cotton gloves.
If these gloves are recycled, there is the potential for even greater reductions in their carbon footprints. These reductions depend on the assumption that the recycled material displaces virgin material and so avoids the emissions associated with virgin material production. Collecting and separating plastics and rubbers for recycling does not guarantee that manufacturers will buy them; depending on market conditions, recyclable materials may be sent to landfills because they cannot compete economically with virgin materials. Collecting, sorting, cleaning, and transporting recyclable materials also requires energy and thus releases emissions that have to be accounted for. In addition, much recyclable material is not used to make the same products but is instead “downcycled” into a product of lesser value or material performance. So, recycling, if it happens at all, does not fully avoid the emissions of creating the original material. In the USA for example, recycling waste rubber has on average only 10% of the carbon benefits of making the original product (EPA 2022).
Finally, global warming is not the only environmental concern. Water consumption is another important factor to consider when assessing sustainability, particularly water use in areas of the world experiencing water scarcity. Here again, the cotton glove has much higher water consumption over its life cycle, totaling more than 400 liters, compared to less than 0.5 liters each for the nitrile or latex gloves. This very large difference is due mostly to the intensive irrigation used in cotton cultivation, particularly in India.
Figure 7 shows the LCA results for cotton, synthetic latex, and nitrile gloves for the full suite of environmental impact categories covered in the TRACI model of the USEPA (not enough data on natural latex was available to model impacts other than global warming). The calculations are done per use of each glove, similar to Figure 6, so including the washing step for the cotton gloves. The results show that cotton gloves have the highest impacts in most, but not all categories. Latex gloves have the highest impacts in fossil fuel use, stemming from their petrochemical feedstocks, and for emissions of smog-forming compounds during production of the raw materials.
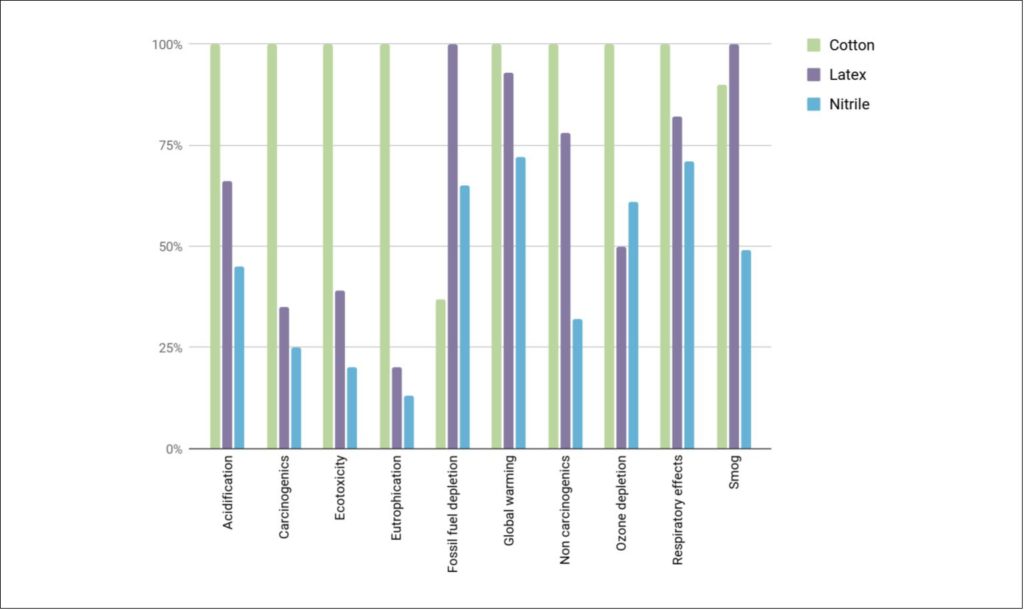
Discussion and Implications
The results shown above have several implications for practice. Most obviously, in situations where all glove types would be acceptable for use in terms of protection, nitrile or natural latex gloves are environmentally preferred in terms of carbon emissions. Reusing these disposable gloves will further decrease their footprints. Recycling disposable gloves (where take-back programs are available) is better than landfilling or incineration, but does not fully avoid virgin material emissions and so is not as good as reuse.
The best option environmentally is to reduce glove use overall, thus avoiding any emissions. This does not mean advocating for gloveless handling in situations that are potentially dangerous to conservators or to objects, but rather for instituting practices that avoid unnecessary glove use. Ordering tasks in a way that allows immediate or continuous reuse of gloves allows users to avoid multiple regloving steps. Hand washing and removing jewelry before handling could also allow for handling some objects gloveless.
Despite the relatively large carbon and water footprints of cotton gloves, there are measures that can be taken to reduce their impacts and even make them competitive with the disposable options. As seen in Figure 6, the largest impact per use of cotton gloves is for washing, whereas the actual materials and manufacturing emissions are approximately equal to the other glove options. Washing cotton gloves in cold water with a mild detergent can reduce washing emissions dramatically.
Furthermore, reusing the cotton gloves more times would have environmental benefits. Approximately 15% of respondents to the AIC member survey reported reusing gloves 7 or more times between each wash; applying this value instead of the average of 4 times would further lower manufacturing emissions by a half to two-thirds. Importantly, if both cold washing and additional reuse were undertaken, then the cotton gloves could be preferable to nitrile.
This case study is meant to be representative but not exhaustive. There are other types of gloves and use scenarios that are possible, and innovative new materials are becoming commercially available. To evaluate whether or not such alternatives are green options, they should ideally be evaluated using a similar framework to that shown in this case study, looking across the life cycle of each option.
A NOTE ABOUT BIOPLASTICS AND BIODEGRADABILITY
Biodegradable nitrile gloves made from a range of bioplastics have recently been developed, promising environmental benefits compared to synthetic nitrile gloves. While bio-based and biodegradable terms are often used interchangeably, they are two distinct attributes of materials that have very different environmental implications. Not all bio-based materials are biodegradable, and not all biodegradable materials are bio-based, though many are.
Bio-based plastics are made from renewable, naturally occurring feedstocks such as corn, wheat, potatoes, soy, tapioca, coconut, cassava, sugar cane, wood and other plants. One of the most common bioplastics is polylactic acid (PLA), made from lactic acid, which is a fermentation product of corn or cane sugars. Bio-based materials can substitute for those derived from petrochemicals; however, producing these materials can involve depleting processes that merely shift environmental burdens. For example, the feedstock of bio-based plastics is often corn, produced through energy-intensive, non-biodiverse farming and relying on synthetic fertilizers derived from fossil fuels (Plamondon et al 2017). Where, when, and how the feedstock is grown can affect its environmental footprint, in contrast to the more static results for synthetic materials that are typically produced using the same industrial process worldwide. So, not all bio-based materials are created equal. Additional certifications such as organic can help indicate environmental preference during cultivation and production process.
In contrast, biodegradable materials influence emissions at end of life. ASTM and ISO have specified testing procedures carried out by third parties such as the Biodegradable Products Institute (BPI 2020), who certify items as biodegradable or compostable. For a product to be considered biodegradable, it must decompose entirely through interaction with microorganisms such as bacteria, fungi, and algae. In contrast, compostable items biodegrade under specific conditions into a soil conditioning material (compost) and leave no toxins behind. Commercial composting operations maintain tightly controlled heat, humidity, and aeration that can be difficult to maintain at home composting operations. Therefore, an item that is certified as ‘industrially compostable’ may not be appropriate for a home composter.
The most common mode of disposal for nitrile and latex gloves is through incineration or in landfills. A small percent of gloves (only those not contaminated with medical waste) are sent for recycling. Recycling plastics, including nitrile gloves, requires energy for transport of the disposed items to the processing centers, sorting, and redistribution to processing plants where the plastic is “transformed” into the downcycled product. A nitrile glove is not typically recycled into another nitrile glove but is more commonly downcycled into a rubberized powder used in less valuable materials such as flooring tiles or rubber crumb surfaces. (TerraCycle)
Conclusion
The cultural heritage sector can push for materials and supplies that are produced in a more environmentally sustainable manner. Around the world, manufacturers are shifting to greener practices, either in response to external pressure, or for economic reasons, or simply because it aligns with internal values. Cultural heritage professionals can choose gloves that are made with sustainably sourced materials (as conveyed through certifications such as the Global Organic Textile Standard for cotton) or using renewable energy sources, or request these options if they are not currently available.
Of course, environmental considerations exist alongside issues of cost, safety, and performance, and are often not the primary concern. As noted by Simons and Kiser (2020), “locating a collection care product that balances the triple weighted scale of sustainability – economy, society, and environment – is difficult in today’s global economy… Ultimately, product choice is an act of compromise.”
PROJECT TEAM
Authors: Shannon Nortz – SN Musæum Methods, LLC
Collaborators: Matthew Eckelman, Sarah Nuberg, Sarah Sutton – STiCH
LCA Modeling Students: Aidan Travers, Corey Kershaw, Emily Eastman, Krissy Govertsen, Sarah Hossain, and Ying Wang
Figures and illustrations: Varnika Kundu, Hyunah Oh, Eric O’Toole, Shraddha Ramani
PROJECT HISTORY
Organized efforts to introduce LCA to U.S. cultural heritage preservation professionals began in 2012 with a series of six LCA case studies conducted as a collaboration between conservators and environmental engineers, in partnership with the MFA Boston. FAIC was awarded a Tier I grant in 2016 and a Tier II grant in 2020 from the National Endowment for the Humanities to expand the case study research and develop a carbon calculator for individual materials under the project Sustainability Tools in Culture Heritage, STiCH,9 available to visitors to the AIC website.10
References
ASTM D6400-12 (2021) “Standard Specification for Labeling of Plastics Designed to be Aerobically Composted in Municipal or Industrial Facilities,” ASTM International : West Conshohocken, PA https://www.situbiosciences.com/product/astm-d6400-compostable-produc-test-composting/
BPI Biodegradable Product Institute. https://bpiworld.org
888c 8th Ave #141 – New York. Accessed August 30, 2021.
de Silva, M. & Henderson, J. 2011. Sustainability in conservation practice. Journal of the Institute of Conservation, 34:1, 5-15.
ecoinvent. 2020. “Systems Models in ecoinvent 3: Allocation at the Point of Substitution.” Accessed August 2, 2022. https://www.ecoinvent.org/database/system-models-in-ecoinvent-3/apos-system-model/allocation-at-the-point-of-substitution.html.
EPA. 2012. Tool for Reduction and Assessment of Chemicals and Other Environmental Impacts (TRACI). United States Environmental Protection Agency. https://www.epa.gov/chemical-research/tool-reduction-and-assessment-chemicals-and-other-environmental-impacts-traci.
EPA. 2022. Waste Reduction (WARM) model v.15. US Environmental Protection Agency. https://www.epa.gov/warm
Environmental Paper Network. 2021. “Paper Calculator: presented by environmental paper network.” Accessed August 2, 2022. https://c.environmentalpaper.org/.
Fava, J.A., and Society of Environmental Toxicology and Chemistry. 1991. A technical framework for life-cycle assessment: Workshop report. August 18-23, 1990. N.p.: SETAC.
GreenDelta. 2020. “openLCA.” Accessed August 2, 2022. https://www.openlca.org/.
International Organization for Standardization. 2006. Environmental management – Life cycle assessment – Requirements and guidelines. 2006-07-01 ed. International Standard, ISO 14044. Geneva: ISO. https://www.iso.org/standard/38498.html.
Jamal, H., Lyne, A., Ashley, P., & Duane, B. 2021. Non-sterile examination gloves and sterile surgical gloves: which are more sustainable?. Journal of Hospital Infection, 118, 87-95.
Kimberly-Clark. 2022. The RightCycleTM Program. https://www.kcprofessional.com/en-us/solutions/rightcycle-by-kimberly-clark-professional
OSHA. 2004. Glove Selection Chart, in Personal Protective Equipment. United States Occupational Safety and Health Administration. http://www.osha.gov/Publications/osha3151.pdf.
Plamondon, C. J. Sinha. 2017. Life Without Plastic. Salem MA: Page Street Publishing.
Rizan, C., Reed, M., & Bhutta, M. F. 2021. Environmental impact of personal protective equipment distributed for use by health and social care services in England in the first six months of the COVID-19 pandemic. Journal of the Royal Society of Medicine, 114(5), 250-263.
Simmons, J. E., & Kiser, T. M. 2020. MRM6: Museum registration methods. Lanham, MD: American Alliance of Museums Press.
Southwick, C. 2019. “Sustainability in Conservation: Saving Our Heritage and Our Planet” (blog post). International Institute for Conservation of Cultural and Historic Works (IIC). https://www.iiconservation.org/content/sustainability-conservation-saving-our-heritage-and-our-planet.
sphera. 2020. “GaBi Packaging Calculator – Sustainable Packaging Design.” Accessed August 2, 2022.
https://gabi.sphera.com/international/software/gabi-envision/gabi-packaging-calculator/.
Stephens, C., E. Breitung, C. Geiculescu, T. Strange. 2022. “Determination of Nitrile Gloves Appropriate for Use When Dry Handling Art.” Journal of the American Institute for Conservation, 61 (3) 162-171.
Sutton, S. & Wylie, E. 2013. The Green Museum: A Primer on Environmental Practice, 2nd ed. Lanham, MD: AltaMira Press.
TerraCycle. 2022. Safety Equipment and Protective Gear – Zero Waste Box™. https://shop.terracycle.com/en-US/products/safety-equipment-and-protective-gear-zero-waste-boxes
United Nations Environment Programme (UNEP). 2005. Life Cycle Approaches: the Road from Analysis to Practice. N.p.: UNEP/SETAC, Life Cycle Initiative, Paris.
Vignon, Bruce W., D. Tolle, B. Cornaby, H. Latham, C. Harrison, T. Boguski, R. G. Hunt, and J. Sellers, and USEPA. 2020. “Life-cycle assessment: Inventory guidelines and principles.” N.p.: CRC Press.
One reply on “Nitrile, Latex & Cotton Gloves”
Thank you all for this wonderful contribution to the field. It was a pleasure to read and a great example of the complexity of sustainability. Not one answer fits all solutions.
In my careful read through, I wonder if Figure 7 may be mislabeled: The text reads “Nitrile gloves have the highest impacts in fossil fuel use,” but in Figure 7 purple has the highest fossil fuel use, which is labeled as latex. I share this in hopes of clarifying any confusion.
Again, thank you for this work!